荷兰的价值驱动维修(VDM): 你了解多少?
更新时间:2015-08-19
文/张洪飞
越来越多的企业已经或者正在引进精益生产方式,不管是离散型企业,还是流程型企业,他们或多或少地应用精益生产工具或精益思想为企业创造价值、消除浪费。虽然,作为制造企业基础的设备管理部门,大多也都在尝试采用精益思想来尽可能地消除浪费、提高设备利用率,然而,设备管理的基础地位(保障生产,不直接产生价值)的性质却没有改变,这一性质决定了设备管理者很难解答如果用在设备管理上的投入减少1%,能给企业带来多少损失的疑问?而这恰恰是企业管理者十分关心的,没有哪个企业管理者会愿意投入更多的钱却得不到相应的回报,但是VDM(Value Driven Maintenance)价值驱动维修却可以给出答案。
VDM是由荷兰的马克·哈曼(Mark Haarman)为代表的设备管理咨询团队提出的一种维修管理理论和实践。它强调用价值理论来衡量维修组织的活动,即维修组织为企业创造的价值应该用其创造的“未来现金流”来衡量。企业为维修组织多投入1%的资源,需要获得更多的未来现金流;反之,企业减少投入的现金流,也期望未来现金流不减少或少减少。该理论认为,维修组织可以从资产利用、成本控制、安全健康环境及资源配置这4个方面为企业创造价值。因此,这4个方面被称之为价值驱动因素。如图1所示。
图1
其中资产利用和成本控制是最基本的价值,设备管理的核心就在于提高资产利用率、降低维护成本;同时还要兼顾职业健康环保和生产安全;合理的资源配置也是维修管理价值的主要体现。
维修组织的价值计算可以借助经济学理论中的现值公式,将其转化为VDM的价值计算公式:
PVm=Σ{ FHSE,t×(CFAU,t+CFCC,t+CFRA,t+CFHSE,t)/(1+r)t }
式中:PVm——潜在的设备维修现值;
FHSE,t——第t年的HSE因子;
CFAU,t——第t年资源利用率创造的未来自由现金流;
CFCC,t——第t年成本控制创造的未来自由现金流;
CFRA,t——第t年资源配置创造的未来自由现金流;
CFHSE,t——第t年HSE方面创造的未来自由现金流;
r——贴现率。
VDM理论通过价值驱动因素分析和最有价值维修组织设计的两阶段8步骤来提高企业的设备管理水平。
价值驱动因素分析阶段通过设定关键指标来测量绩效,通过与行业企业的比较来设定基准,通过计算4个价值驱动因素来找到主要的价值驱动因素。
最有价值维修组织设计阶段则根据第一阶段的结果来确定核心能力,围绕核心能力来设计最有价值的维修组织,进而优化流程、人员配置和信息化支持,通过监测来衡量改善的效果。如图2所示。
图2
需要指出的是,最具改善价值的核心能力的改善过程需要借助当前普遍认可的最佳实践模型来实现。例如:提高资产利用率,可以借助TnPM全面规范化生产维护来实现;提高可靠性,则可以借助以可靠性为中心的维护(Reliability Centered Maintenance)来实现。
至今,VDM已经在全球超过100家工厂(包括造纸、水泥、汽车制造等行业)应用并取得良好的效果。
综上所述,VDM实质上是围绕价值创造开展的一个系统改善过程,是建立在设备管理最佳实践基础上的。它通过经济学理论把设备管理的价值量化,从而为设备管理的精益化提供了保障,精益管理的价值和浪费都能够在宏观的现金流变动中得到最实在的体现。
VDM纠正了以往单纯为了改善而改善的弊端,确定了围绕目标集中改善的管理思想。把有限的精力聚焦到最有价值的事情上来,是设备管理精益化和科学化的有力武器。
(中国设备管理协会国际合作交流中心供稿)
the Netherlands Value Driven Maintenance(VDM)
VDM is a philosophy and practice for maintenance proposed by the equipment management consultancy lead by Mark Haarman. It emphasizes the way to measure maintenance activities with the theory of value, that is to say, the value created by maintenance organization should be measured by the future cash flow. The enterprise will get more future cash flow with additional 1% input for maintenance. On the contrary, the enterprise expects to get the same future cash flow or the valuable deduction with less input for maintenance. The VDM represents that the maintenance organization can create value from the four aspects: Asset Utilization, Cost Control, Health & Safety & Environment, and Resource Allocation, which are called as Value Driver. The figure follows.
What should be mentioned is the realization of the improvement process of core competence of most improved value relies on the best practice model that currently and widely accepted. For example, the TnPM will improve asset utilization; the RCM (Reliability Centered Maintenance) will improve reliability.
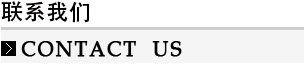
社长兼主编:陈雪芹
电 话:(010)68515135
编辑部
电 话:(010)68054816/68054837/68054838/68054839
运营部
电 话:(010)68052048
学术稿件咨询电话:
电 话:(010)64936065
新闻投稿邮箱:
zgsbgcxw@126.com
技术文章投稿邮箱:
zgsbgc@126.com
开户行
工行北京礼士路支行
户 名
《中国设备工程》杂志社
账 号
0200 0036 0902 2100 604
地 址
北京市西城区三里河一区12号楼4门3层(100045)